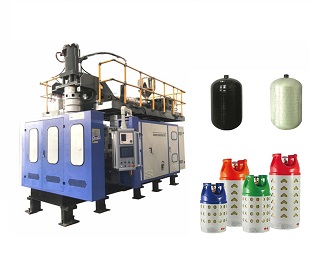
The production line for composite LPG (Liquefied Petroleum Gas) cylinders is a manufacturing process specifically designed to produce lightweight and durable LPG cylinders made from composite materials. These cylinders are typically used for storing and transporting LPG, which is commonly used as a fuel for cooking, heating, and various industrial applications.
The specific process details:
Inner liner blow molding, shaft loading by robot automatically, robot hanging inner liner to inner liner frame, robot grabbing inner liner to winding machine automatically, full automatic winding, robot grabbing inner liner to fiberglass winding machine for outer protective layer winding, robot grabbing inner liner automatically that has already wrapped protective layer to chain curing furnace, shell solidification completed,shaft unloading by robot automatically, finished-product airtightness detection experiment, finished-product water pressure blasting experiment, finished product completion.
Here's a general overview of the composite LPG cylinder production line:
Material Selection: The production process begins with the selection of high-quality composite materials, often consisting of a combination of fiberglass and resin. These materials provide the necessary strength and corrosion resistance for LPG storage.The specific materials including PE,glass fibre,resin,metal+PE (valve boss),modified HDPE.
Cylinder Fabrication: HDPE material is blown into a cylindrical shape of a certain volume size, and then glass fiber is wound onto the surface of the cylindrical cylinder to form a cylindrical structure. The cylinder will have a plastic protective shell to protect its inner liner, which is usually extruded.
Resin Application: A resin is applied to the layers of composite material to bond them together and provide additional strength. The resin is usually cured or hardened using heat and pressure to ensure a secure bond.
Valve Installation: Once the basic cylinder structure is formed, the production line incorporates the necessary components, such as valves, pressure relief devices, and safety features. These components are securely attached to the cylinder.
Quality Control: Throughout the production process, quality control measures are in place to ensure that each cylinder meets the required safety standards and specifications. This includes pressure testing, leak testing, and visual inspections.
Coating: The cylinders are often coated with protective layer to enhance their aesthetics and protect them from environmental factors.
Final Testing: Before the cylinders are considered ready for distribution, they undergo a final round of testing to verify their safety and integrity. This includes checking for any defects or imperfections.
Packaging and Distribution: Once the cylinders pass all quality control checks, they are packaged for distribution and shipped to customers or distributors.
The use of composite materials in LPG cylinder production offers several advantages, including reduced weight, increased corrosion resistance, and improved safety. These composite cylinders are often preferred for their portability and durability, making them a popular choice for various LPG applications.
It's worth noting that specific production processes and technologies can vary among manufacturers, but the general steps outlined above provide an overview of how composite LPG cylinders are typically produced.
The specific process details:
Inner liner blow molding, shaft loading by robot automatically, robot hanging inner liner to inner liner frame, robot grabbing inner liner to winding machine automatically, full automatic winding, robot grabbing inner liner to fiberglass winding machine for outer protective layer winding, robot grabbing inner liner automatically that has already wrapped protective layer to chain curing furnace, shell solidification completed,shaft unloading by robot automatically, finished-product airtightness detection experiment, finished-product water pressure blasting experiment, finished product completion.
Here's a general overview of the composite LPG cylinder production line:
Material Selection: The production process begins with the selection of high-quality composite materials, often consisting of a combination of fiberglass and resin. These materials provide the necessary strength and corrosion resistance for LPG storage.The specific materials including PE,glass fibre,resin,metal+PE (valve boss),modified HDPE.
Cylinder Fabrication: HDPE material is blown into a cylindrical shape of a certain volume size, and then glass fiber is wound onto the surface of the cylindrical cylinder to form a cylindrical structure. The cylinder will have a plastic protective shell to protect its inner liner, which is usually extruded.
Resin Application: A resin is applied to the layers of composite material to bond them together and provide additional strength. The resin is usually cured or hardened using heat and pressure to ensure a secure bond.
Valve Installation: Once the basic cylinder structure is formed, the production line incorporates the necessary components, such as valves, pressure relief devices, and safety features. These components are securely attached to the cylinder.
Quality Control: Throughout the production process, quality control measures are in place to ensure that each cylinder meets the required safety standards and specifications. This includes pressure testing, leak testing, and visual inspections.
Coating: The cylinders are often coated with protective layer to enhance their aesthetics and protect them from environmental factors.
Final Testing: Before the cylinders are considered ready for distribution, they undergo a final round of testing to verify their safety and integrity. This includes checking for any defects or imperfections.
Packaging and Distribution: Once the cylinders pass all quality control checks, they are packaged for distribution and shipped to customers or distributors.
The use of composite materials in LPG cylinder production offers several advantages, including reduced weight, increased corrosion resistance, and improved safety. These composite cylinders are often preferred for their portability and durability, making them a popular choice for various LPG applications.
It's worth noting that specific production processes and technologies can vary among manufacturers, but the general steps outlined above provide an overview of how composite LPG cylinders are typically produced.