OKSK640 CNC Spinning Machine
OKSK640 CNC Spinning Machine
A CNC spinning machine, also known as a CNC metal spinning machine or a CNC metal spinning lathe, is a computer-controlled machine used in metalworking to form sheet metal or other thin-walled materials into a variety of shapes. It is a specialized type of machine tool used in manufacturing processes, and it's particularly useful for producing hollow, symmetrical, and conical shapes such as domes, cones, and cylindrical parts with high precision.
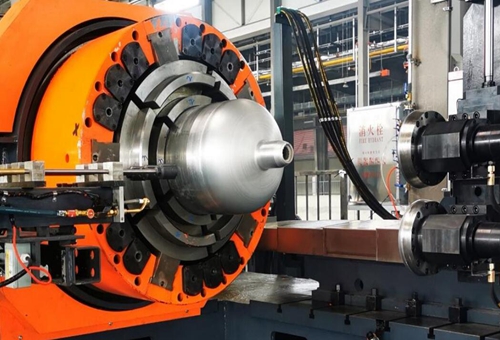
Cylindrical blank diameter Max.640mm
Cylindrical blank length Max.3200mm
Machinable thickness range 6061 25mm
X-axis displacement 500mm
Z-axis displacement 900mm
X,Z axis maximum movement speed 4000mm/min
Rated thrust 140KN
Axial positioning accuracy 0.04mm
Repeated positioning accuracy 0.02mm
Spindle speed 0-500rpm
Spindle power 110KW
Hardware Configuration
Control mode:Siemens 828D CNC system
Feed power: Siemens servo motor
Drive control: Siemens S120
Heating method: Flame gun heating (Propane+Oxygen or Natural Gas+Oxygen)
Equipment area: 10 meters * 5.5 meters * 2.3 meters
Weight 26 ton
Installed power: 140KW
Strong Flow Forming
Hydrogen gas cylinder blanks are generally prepared using reverse extrusion technology. Due to process limitations, the wall thickness is generally relatively thick, usually around 18-24 millimeters. Hydrogen gas cylinders require a wall thickness of around 5-7 millimeters, and the closing part of the bottle mouth generally needs a thickness of 10-12 millimeters. Therefore, it is necessary to perform strong rotation on thicker blanks.
Strong spinning usually uses a three wheel spinning machine for multi pass spinning. The thickness of the raw material is determined based on the minimum thickness of the product, and it is generally suitable to control it at a thinning rate of about 70%.
Before spinning, the raw material must have a smooth inner and outer surface, without any defects such as scratches or bumps. In general, it is advisable for the weight of the raw material to be equal to the weight of the finished product plus a length of 60mm of raw material of tube. After spinning, the pipe material is required to have no defects such as slag inclusion, peeling, and internal scratches.
Pipe material after flow forming:
1. The inner and outer surfaces of the strong rotary tube blank should be smooth, without cracks, corrosion, inclusions, peeling, bubbles, scratches, bumps, scratches, folds, straight lines, pits and other defects
2. Internal surface quality requirements, roughness Ra2.0, no defects such as cracks, dents, heavy skin, bumps, scratches, etc. on the surface, and consistent polishing patterns on the inner wall (circumferential)
3. The straightness of the strong rotary tube shall not exceed 0.15%
4. The deviation between the average inner diameter of the strong spiral tube and the nominal outer diameter shall not exceed 1% of the nominal outer diameter
5. The difference between the maximum and minimum diameters on the same section of the strong spiral tube exceeds 2% of the average outer diameter of that section
6. Each strong rotary tube shall be inspected and recorded according to the diagram, and inspection documents shall be provided
7. The macrostructure of the strong rotary tube meets the requirements of GB/T4437, and the grain size is not lower than level-2
Strong Flow Forming Machine for Raw Materials
Technical requirements and related parameters
Equipment: Three wheel flow forming machine
Effective diameter of rotary press: 600mm/800mm
Effective length of rotary press: maximum 3200mm
Forming method: Three wheel flow forming
Forming temperature: room temperature, special coolant
Spinning Closure(Cylindrical blank shrink):
Spinning closure is the process of heating and spinning both ends of a pipe material. Due to the need for thread processing inside the small mouth after spinning, and to ensure the strength of the mouth, the thickness of the small mouth after spinning needs to be maintained at around 20mm. Therefore, the thickness of the closing end of the blank pipe is also relatively thick. The hot spinning process is used for the necking of the spinning, and it is necessary to maintain a relatively uniform temperature at the necking area during spinning. The temperature should generally be controlled between 350C-450C, and should not be too high for a long time to prevent coarse material grains from affecting the strength performance of the gas cylinder.
Spinning Closure(Cylindrical blank shrink)
1.The nominal volume of the aluminum alloy inner liner is 210L, and the head surfaces at both ends are symmetrical and consistent with the bottle mouth structure and threads
2.The front and bottom of the aluminum alloy inner liner adopt a gradient thickness design, with smooth transitions between the cylinder and the front, as well as between the cylinder and the bottom
3.The thread of the aluminum alloy liner is 2-12UN-2B, and the dimensions and manufacturing tolerances should comply with GB/T20668 Unified Thread;The requirement is that the surface of the thread should be smooth, and there should be no inverted or disordered teeth;The effective length of the thread should not be less than 22mm
4.The inner and outer surfaces of the aluminum alloy liner are free from visible surface indentation, protrusions, overlaps, cracks, and inclusions;The transition part between the neck and the end is free from sudden changes or obvious wrinkles, and the transition between the cylinder and the end is smooth
5.If surface defects are removed by machining or mechanical grinding, the defect removal area should have a smooth transition and the wall thickness should not be less than the minimum design wall thickness
6.Mark the aluminum inner liner number clockwise on any bottle back end face (near the outer circle) of the aluminum alloy inner liner (to ensure traceability), with a font height of 5-8 and a depth of no more than 0.3mm, with clear marking
7.The deviation between the maximum outer diameter and the maximum inner diameter on the same section of the cylinder shall not exceed 2% of the nominal diameter, and the straightness of the cylinder shall not exceed 0.3% of its length
Hot Spinning
Technical requirements and parameters
Spinning equipment: Special CNC spinning machine
Maximum shrink diameter: 480,640
Maximum length: 3500mm
Spining temperature: 350~450C
Heating method: Flame
Single cylinder time: 12 minutes * 2 ends
Loading and unloading method: Robotic arm
Setup: A metal disk or sheet is securely clamped in the machine's chuck or workpiece holder. The operator specifies the desired shape and dimensions through a computer program or software that controls the machine.
Spinning: The machine's spinning tool, also known as the mandrel or roller, comes into contact with the metal workpiece. The workpiece rotates at a high speed while the spinning tool moves along its surface. The tool exerts pressure on the metal, causing it to gradually flow and take the shape of the desired part.
Computer Control: The CNC aspect comes into play here. The machine is computer-controlled, which means it follows precise instructions from the software to shape the metal accurately. The CNC system controls the tool's movements, rotation, and pressure to create the desired shape.
Final Product: As the spinning tool moves along the workpiece, it forms the metal into the desired shape. This process continues until the entire part is formed. Once complete, the finished part can be removed from the machine.
Strong Flow Forming
Hydrogen gas cylinder blanks are generally prepared using reverse extrusion technology. Due to process limitations, the wall thickness is generally relatively thick, usually around 18-24 millimeters. Hydrogen gas cylinders require a wall thickness of around 5-7 millimeters, and the closing part of the bottle mouth generally needs a thickness of 10-12 millimeters. Therefore, it is necessary to perform strong rotation on thicker blanks.
Strong spinning usually uses a three wheel spinning machine for multi pass spinning. The thickness of the raw material is determined based on the minimum thickness of the product, and it is generally suitable to control it at a thinning rate of about 70%.
Before spinning, the raw material must have a smooth inner and outer surface, without any defects such as scratches or bumps. In general, it is advisable for the weight of the raw material to be equal to the weight of the finished product plus a length of 60mm of raw material of tube. After spinning, the pipe material is required to have no defects such as slag inclusion, peeling, and internal scratches.
Pipe material after flow forming:
1. The inner and outer surfaces of the strong rotary tube blank should be smooth, without cracks, corrosion, inclusions, peeling, bubbles, scratches, bumps, scratches, folds, straight lines, pits and other defects
2. Internal surface quality requirements, roughness Ra2.0, no defects such as cracks, dents, heavy skin, bumps, scratches, etc. on the surface, and consistent polishing patterns on the inner wall (circumferential)
3. The straightness of the strong rotary tube shall not exceed 0.15%
4. The deviation between the average inner diameter of the strong spiral tube and the nominal outer diameter shall not exceed 1% of the nominal outer diameter
5. The difference between the maximum and minimum diameters on the same section of the strong spiral tube exceeds 2% of the average outer diameter of that section
6. Each strong rotary tube shall be inspected and recorded according to the diagram, and inspection documents shall be provided
7. The macrostructure of the strong rotary tube meets the requirements of GB/T4437, and the grain size is not lower than level-2
Strong Flow Forming Machine for Raw Materials
Technical requirements and related parameters
Equipment: Three wheel flow forming machine
Effective diameter of rotary press: 600mm/800mm
Effective length of rotary press: maximum 3200mm
Forming method: Three wheel flow forming
Forming temperature: room temperature, special coolant
Spinning Closure(Cylindrical blank shrink):
Spinning closure is the process of heating and spinning both ends of a pipe material. Due to the need for thread processing inside the small mouth after spinning, and to ensure the strength of the mouth, the thickness of the small mouth after spinning needs to be maintained at around 20mm. Therefore, the thickness of the closing end of the blank pipe is also relatively thick. The hot spinning process is used for the necking of the spinning, and it is necessary to maintain a relatively uniform temperature at the necking area during spinning. The temperature should generally be controlled between 350C-450C, and should not be too high for a long time to prevent coarse material grains from affecting the strength performance of the gas cylinder.
Spinning Closure(Cylindrical blank shrink)
1.The nominal volume of the aluminum alloy inner liner is 210L, and the head surfaces at both ends are symmetrical and consistent with the bottle mouth structure and threads
2.The front and bottom of the aluminum alloy inner liner adopt a gradient thickness design, with smooth transitions between the cylinder and the front, as well as between the cylinder and the bottom
3.The thread of the aluminum alloy liner is 2-12UN-2B, and the dimensions and manufacturing tolerances should comply with GB/T20668 Unified Thread;The requirement is that the surface of the thread should be smooth, and there should be no inverted or disordered teeth;The effective length of the thread should not be less than 22mm
4.The inner and outer surfaces of the aluminum alloy liner are free from visible surface indentation, protrusions, overlaps, cracks, and inclusions;The transition part between the neck and the end is free from sudden changes or obvious wrinkles, and the transition between the cylinder and the end is smooth
5.If surface defects are removed by machining or mechanical grinding, the defect removal area should have a smooth transition and the wall thickness should not be less than the minimum design wall thickness
6.Mark the aluminum inner liner number clockwise on any bottle back end face (near the outer circle) of the aluminum alloy inner liner (to ensure traceability), with a font height of 5-8 and a depth of no more than 0.3mm, with clear marking
7.The deviation between the maximum outer diameter and the maximum inner diameter on the same section of the cylinder shall not exceed 2% of the nominal diameter, and the straightness of the cylinder shall not exceed 0.3% of its length
Hot Spinning
Technical requirements and parameters
Spinning equipment: Special CNC spinning machine
Maximum shrink diameter: 480,640
Maximum length: 3500mm
Spining temperature: 350~450C
Heating method: Flame
Single cylinder time: 12 minutes * 2 ends
Loading and unloading method: Robotic arm
Cylindrical blank diameter Max.640mm
Cylindrical blank length Max.3200mm
Machinable thickness range 6061 25mm
X-axis displacement 500mm
Z-axis displacement 900mm
X,Z axis maximum movement speed 4000mm/min
Rated thrust 140KN
Axial positioning accuracy 0.04mm
Repeated positioning accuracy 0.02mm
Spindle speed 0-500rpm
Spindle power 110KW
Hardware Configuration
Control mode:Siemens 828D CNC system
Feed power: Siemens servo motor
Drive control: Siemens S120
Heating method: Flame gun heating (Propane+Oxygen or Natural Gas+Oxygen)
Equipment area: 10 meters * 5.5 meters * 2.3 meters
Weight 26 ton
Installed power: 140KW