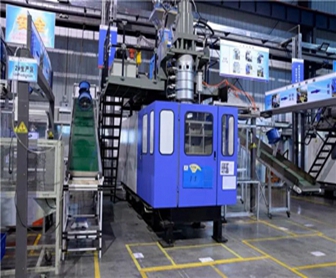
High density polyethylene liner fully wrapped glass fiber reinforced composite LPG cylinder production line
It is also called type IV composite LPG cylinder production line,this intelligent production lines adopt integrated design methods, in-situ forming processes, and flexible winding equipment, which can improve the structural efficiency of fiber winding products by 10-15%. The research results can be applied to the efficient manufacturing of composite material gas cylinders such as,CNG,LNG,LPG,Hydrogen.
Manufacturing of composite gas cylinders:
The main function of the fiber reinforced layer of composite gas cylinders is to withstand pressure, so the fiber layer has a significant impact on the mechanical properties of composite materials when manufacturing composite gas cylinders, the main factors considered for the fiber reinforced layer include the winding tension of the gas cylinder, the laying sequence, the winding angle, the winding thickness, and the wire type of the fiber winding.
During the winding manufacturing process of composite gas cylinders, a certain amount of tension needs to be applied to the fibers. On the one hand, it is to arrange the fibers according to the design line on the inner liner, and on the other hand, it is to generate a certain degree of prestress on the inner liner and winding layer of the gas cylinder, thereby improving the fatigue resistance of the gas cylinder,Research and development personnel Chen Ruxun proposed that the important reason for affecting the strength of fibers is the uneven force distribution of fibers along the thickness direction of the gas cylinder, and the winding tension is an important factor for the uneven force distribution of fibers, especially for gas cylinders with thicker walls; Therefore, how to reasonably control the winding tension is an important link in improving the strength of gas cylinder fibers Engineer Zhang Zongyi et al. proposed an equivalent cooling method, which equates the pre-stress generated by winding tension to the pre-stress generated by composite material layer cooling. The effect of winding tension on the stress of circumferential winding composite material gas cylinders was studied using finite element software The research results indicate that as the winding prestress increases, the working stress of the inner liner of the circumferential winding composite material gas cylinder decreases, and the working stress of the composite layer increases. When the prestress generated by the winding tension is large, it will counteract the effect of the self tightening process,Wang Xinrong, an engineer, studied the influence of winding tension on the bursting pressure of carbon fiber wound aluminum liner composite cylinder. The simulation results showed that the bursting pressure of the cylinder with winding tension was 3.03% higher than that of the cylinder without winding tension. Cohen used experimental design methods to determine the influence of fiber prestress on the structural mechanics performance of winding during the winding process, It was found that increasing prestress can effectively increase the volume percentage of fibers in the winding layer of the fiber winding structure, thereby improving the strength of the structure.
Kalaycioglu et al. studied the Kevlar fiber wound 6061-T6 aluminum lined composite gas cylinder, mainly focusing on the influence of symmetrical and asymmetrical laying sequence on the cylinder performance when the winding angle of the fiber changes continuously. The research results show that the symmetrical laying sequence increases the bursting pressure by 15% compared with the asymmetrical laying sequence, mainly because the symmetrical laying sequence makes the stress distribution of the cylinder fiber layer more uniform, Reduced stress concentration Bertin et al. conducted experimental and simulation studies on polymer composite hydrogen storage cylinders, mainly focusing on the influence of the stacking sequence of the composite layer on the mechanical properties of the composite material. The research results showed that the symmetrical stacking sequence had the highest failure stress value Velosa et al. studied composite gas cylinders wrapped with polyethylene lined glass fibers and found that the direction of the fibers, the order of layers, and the number of layers can all affect the strength of the fiber winding layer.
Wild et al. found through grid analysis that the optimal angle for filament wound composite pressure vessels is 54.74 °. Parnas et al. considered the effect of internal pressure on filament wound composite gas cylinders and concluded that the optimal winding angle mainly depends on geometric shape and failure criteria used, And the range of winding angle is given to be 52.1~54.2 °. Rosenow analyzed the stress and strain situation of thin-walled composite containers when the winding angle changes between 15 °~85 ° using classical lamination theory; For cylindrical vessels with a ratio of circumferential stress to axial stress equal to 2, the optimal equilibrium winding angle is 55 ° Erkal et al. conducted experimental research on the fatigue failure of composite pressure vessels with glass fiber wrapped plastic liners. The glass fibers were wrapped in a symmetrical manner, with winding angles of ± 75 °, ± 60 °, ± 55 °, and ± 45 °. The experimental results showed that when the winding angle was ± 55 °, the maximum burst pressure was 10.2 MPa.
The thickness of fiber winding is not necessarily the better. If the fiber winding is too thick, not only will it increase manufacturing costs, but also the strength of the outer layer fibers cannot be fully utilized, resulting in material waste Researcher Gu Haibo designed the circumferential winding thickness of a 2 L carbon fiber wound aluminum liner composite gas cylinder As the thickness of the circumferential fibers increases, the stress levels of the inner liner and fibers decrease under working pressure and minimum burst pressure, while the stress ratio of the fibers decreases According to the DOT-CFFC standard, the range of values for fiber monolayer thickness is 0.13 ≤ t ≤ 0.14 mm.
For fiber winding structures, the linetype of fiber winding is an important design parameter At present, there are three basic types of fiber winding: circumferential winding, longitudinal winding, and spiral winding Circumferential winding is carried out along the circumference of the container and can only be carried out on the cylinder section. The angle of fiber winding is usually between 85 ° and 90 °, and the winding process is simple The fiber trajectory of longitudinal winding is a single circular plane closed curve with a small winding angle, and is mostly used for thick and short containers Spiral winding is also known as geodesic winding. When winding, the wire guide rotates at a constant speed along the mandrel axis at a specific speed. The barrel section and head can be filament wound at a winding angle of about 12 °~70 °. The winding process is complex, Engineers such as Chi Xiufen found through collision damage research that the ability of spiral winding to resist damage is higher than that of ordinary circumferential winding. Therefore, it is recommended to use spiral winding when manufacturing composite pressure vessels In the manufacturing of composite gas cylinders, a spiral and circumferential winding shape is generally used.
Related tags:
indane gas fiber cylinder production line
22 lb composite propane tank equipment
composite propane tank sizes
lpg composite production line
carbon composite cylinders manufacturing equipment
fiberglass propane bottles machine
new composite cylinder equipment
ragasco gas
composite lpg gas cylinder production line
composite gas cylinder manufacturers
viking cylinders 22lb
regasco composite lpg gas bottles line
viking composite propane cylinders workshop
worthington composite cylinders
composite compressed air tanks
fibre cylinder indane
composite propane bottles producing equipment
10 lb composite propane tank production line
The main application in hydrogen, natural gas, liquefied petroleum gas, and industrial gas energy storage and transportation is a key link in energy security and efficient application. Compared with metal energy storage and transportation pressure vessels, advanced composite material pressure vessels have advantages such as lightweight, corrosion resistance, explosion-proof performance, durability, and intelligent scalability.
Therefore, they are widely used in fields such as transportation, energy, chemical, and military.We have researched and developed the "non-metallic inner fiber fully wound composite special pressure cylinder", completing the systematic research on the sealing and structural design of composite gas cylinders successfully, preparing the composite gas cylinder process technology, developing a complete set of intelligent manufacturing production lines for composite gas cylinders, and a complete set of testing and testing equipment for composite pressure vessels, becoming one of the three companies globally capable of providing a complete set of automated production lines for Type IV gas cylinders in the field of composite material equipment manufacturing.
In the company's self-developed core equipment, such as a five station fully automatic vertical winding machine for picking and shearing yarn, and a multi station rotary disc water pressure testing machine, has reached the leading level in China.Our company integrate upstream industry supply chain resources, realizes the closed-loop industrial application of the entire industry chain with independent intellectual property rights as the core, and masters the core technology and overall solution of the entire process from raw materials, production process, manufacturing equipment, and product testing for plastic inner wrapped composite material type IV gas cylinders. At the same time, two Type IV gas cylinder products were finalized, including plastic inner wrapped composite material liquefied petroleum gas cylinders and plastic inner wrapped carbon fiber composite material hydrogen cylinders.
Fully automated production
Cost effective and highly automated manufacturing process
All manufacturing process are fully automated the LPG cylinder is built from raw materials to finished product
1.Blow-Molder
2.Robot
3.Inspection Table
4.Injection Molding Machines
5.Corona/Flame Treatment
6.Spin Welding
7.Resin Feeder
8.Filament Winding Machines
9.Ovens
10.Test Equipment
11.Injection Molding Machines
12.Conveyer Belt
13.Injection Molding Machines
14.Packing,Sub-Assembly
Frequency transformer,Valve,Servo pump,Pneumatic valve,Electronic components,Screw Motor,Bearing,Oil seal,Electronic control system,Gearbox,Air cylinder,all parts and components come from top brand:
Automatic composite cylinder production line
Model: PBI-905X
Single station
Storage type single die head
Single layer
Storage capacity: 5kg
Matching the raw materials of the machine: (Marlex)HDPE or equivalent
Electronic control system: BECKHOFF Germany
Specifications of finished inner liner: 36L 47L
Net weight of finished inner liner: 1.35kg 1.6kg
Molding cycle time: 90±2S,the final cycle is based on the product provided by the customer
Automatic sealing machine 1 set
Automatic overflow removal device 1 set
Thickness control system 100 point,valve MOOG Japan 1 set
Three point combination (automatic periodic filtration of moisture) 1 set
Cooling fixture and fixture device 1 set
Bottom overflow conveyor line (one straight line) 1 set
36L mold (including auxiliary mold) material: 7075 aluminum+cut beryllium copper inlay 1 set
47L mold (including auxiliary mold) material: 7075 aluminum+cut beryllium copper inlay 1 set
General specification:
A、The annual output of this production line is 300,000 pieces,it runs 20 hours a day
B、Total electric power 600KW
C、Production area 2000 ㎡(Storage space excluded)
D、Plant height ≥ 7M,equipment inlet width ≥5M,equipment entry height ≥ 5M
EN standard,CE certified composite LPG cylinder production line.